What is Reciprocating pump?
A reciprocating pump is a kind of fine displacement pump that consists of piston pumps, plunger pumps, and diaphragm pumps. reciprocating pump can final for many years if properly maintained. However, they could put on out if no longer properly maintained.
They are often used while quite small amounts of liquid need to be treated and the release pressure may be very excessive. In a reciprocating pump, the chamber in which the liquid is enclosed is a desk-like cylinder made of a piston or plunger.
A reciprocating pump is a mechanical tool that converts the mechanical strength of a fluid into hydraulic strength (strain power). It uses a piston or plunger to move a liquid from one vicinity to every other. Reciprocating pumps also are referred to as reciprocating pump because they use a piston or plunger to transport the pump.
In this pump, a piston inside the pump cylinder reciprocates between high and low positions. When the piston actions toward the lowest lifeless middle, it draws inside the fluid and while it moves closer to the pinnacle lifeless center, it pressurizes the fluid.
Read more What Is A Hydraulic Pump?
Parts of Reciprocating Pump
The Parts of the Reciprocating Pump are given below:
- Water Sump
- Strainer
- Suction Pipe
- Suction Valve
- Cylinder
- Piston and Piston rod
- Crank and Connecting rod
- Delivery valve
- Delivery pipe
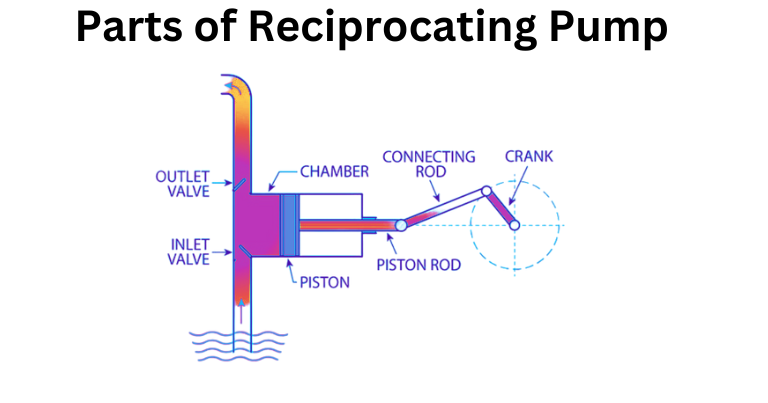
Water Sump
This is the supply of water. Water is transported from the sump to the supply pipe using a piston.
Strainer
It acts as a internet thru which all the dirt, dirt particles and so on may be filtered out. From the oil pan. If there is no strainer, dust and particles may additionally get into the cylinder, inflicting clogging and affecting the functioning of the pump.
Suction Pipe
The major feature of the suction pipe is to accumulate water from the oil pan and direct it into the cylinder through the suction valve. The suction pipe connects the water receiver with the cylinder.
Suction Valve
This is a test valve, it lets in liquid to be taken from the suction line and directed to the cylinder, but it does now not permit water to be placed back there. In this sense, the flow is one-way.
It simplest opens whilst sucking in liquid and closes whilst discharging liquid to the outside.
Cylinder
A hole cylinder fabricated from forged iron or metallic alloy, along with an arrangement of a piston and a piston rod.
Piston and Piston rod
The piston movements backwards in the cylinder to attract in fluid, and the piston actions ahead to expel fluid.
The piston rod allows the piston circulate in a linear path, both h.Forward or backward.
Crank and Connecting rod
The crank is hooked up to the strength source like device, engine and so on for rotation and the connecting rod acts as an middleman among the crank and the piston and converts the rotational motion into linear motion.
Delivery valve
The characteristic of shipping pipe is to transport water from the cylinder to the desired vicinity.
Delivery pipe
Like the suction valve, the stress valve is likewise a test valve. During suction, the suction valve is open and the release valve is closed, and during discharge, the suction valve is closed and the release valve is open to move the liquid.
Reciprocating Pump Application
reciprocating pump are used in:
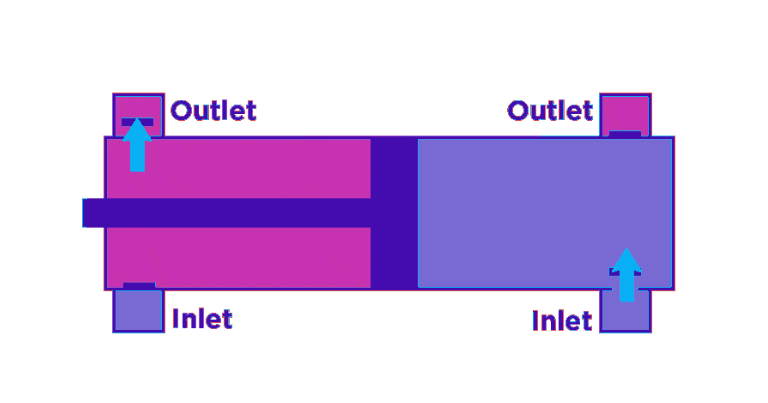
- Cleaning vessels, pipes, tanks, hoses, condensate lines, warmth exchangers and many others.
- Oil drilling, refineries, production, disposal, injection.
- Pneumatic packages.
- Vehicle cleansing.
- Sewer pipe cleansing.
- Wet Sand Blasting
- Feed to Boilers
- High Pressure Pumps for RO Systems (Reverse Osmosis)
- Hydro Testing of Tanks, Containers and so on.
- Fire Fighting Systems.
- Waste Water Treatment Systems.
How does a Reciprocating Pump work?
When a reciprocating pump is powered, the electric motor rotates a crank.
The perspective fashioned through the crank affects the motion of the piston within the cylinder. According to the diagram above, while the crank reaches role A, the piston movements all of the way to the left in the cylinder. H. θ = 0.
Similarly, whilst the crank reaches position C, the piston movements all the manner to the right inside the cylinder. H. θ = one hundred eighty.
As the piston actions toward the proper-most function, a partial vacuum is created in the cylinder. H. (θ = 0 to θ = a hundred and eighty), which draws liquid into the suction line.
This is due to the fact the atmospheric strain of the liquid at the lowest is substantially decrease than the stress within the cylinder. Due to the stress difference, water enters the cylinder through the check valve.

The water closing in the cylinder quantity needs to be despatched to the hole pipe via the outlet valve. This can be completed via turning the crank from C to A. H. (θ=a hundred and eighty to θ=360), causing the piston to move forward.
As the piston movements ahead the strain inside the cylinder will increase and becomes higher than atmospheric strain.
This causes the stress valve to open and the suction valve to shut.
The water that enters the pressure valve can’t drift again into the cylinder because it’s far a one-manner valve or test valve.
From there it enters the strain line and may be directed to the desired place.
In this manner, the water within the oil pan is sucked out and discharged to the desired region by way of the piston inside the cylinder.
Advantages of Reciprocating Pump
- reciprocating pump can provide the required drift price very accurately.
- They offer non-stop transport quotes.
- They can supply fluids at very excessive pressures.
- There is no need to top a reciprocating pump.
- The performance of reciprocating pump is 10-20% better than that of centrifugal pumps.
Disadvantages of Reciprocating Pump
- It is tough to pump viscous beverages with reciprocating pump.
- Pumps include many elements, so preservation fees are very high.
- Flow fee is reduced.
Related FAQ’S
What are the common mistakes with eciprocating pump?
- Pump running backwards/too slow 2) Not enough oil on the pressure aspect
- Too lots oil on the drive facet
- Oil viscosity is inaccurate
- Pump walking at higher than advocated stress 6) Main bearings are too tight.
- The drive is out of alignment.
- The belt is just too tight.
- One or greater exhaust valves are caught open. 10) Insufficient cooling.
What are eciprocating pumps first-rate for?
eciprocating pumps are used whilst particular amounts of liquid have to be pumped and whilst the desired pumping pressure is better than different sorts. The fluid is moved by means of a piston that actions inner a cylinder.
Why do eciprocating pumps now not require priming?
Why does a eciprocating pumps not want suction? If an air bubble is thrown into the cylinder, it will disintegrate at some point of discharge or get away through the exhaust valve due to the fact the suction valve is closed at some stage in the release process, so there may be a very low opportunity of cavitation taking place inside the cylinder.
What is slippage in a eciprocating pumps?
The slippage of a eciprocating pumps is defined as the difference between the theoretical discharge volume and the real discharge volume. The real discharge quantity of a piston pump is less than the theoretical discharge extent due to water leakage for the duration of pump operation.
What is the main function of a eciprocating pumps?
A eciprocating pumps is a nice displacement pump that receives the fluid to be moved into a cavity and expels a hard and fast quantity of fluid using mechanical stress. It is a fixed extent pump that operates in a low flow, high discharge stress surroundings.