Introduction
Spur gears are cylindrical toothed factors utilized in commercial device to transmit mechanical motion and control speed, electricity and torque. These simple gears are cheap, long lasting and reliable, providing a positive consistent pace drive that makes ordinary business duties simpler.
What Is A Spur Gear?
Spur gears or spur gears are the most effective kind of gears. They consist of a cylinder or disc with radially projecting enamel. The teeth aren’t straight and commonly have a special shape to acquire a consistent drive ratio, usually involutes but much less often cycloids, however the part of each tooth is immediately and parallel to the axis of rotation.
Spur gears are the handiest common gears that transmit movement between parallel coplanar enamel which might be instantly and parallel to the shaft. Spur gears are one of the most common sorts of precision cylinders.
These gears function a simple design of straight, parallel tooth organized around a cylinder frame with a relevant hole that fits the shaft.
In many versions the gears are machined with a hub that thickens the equipment body around the bore without converting the gear surface. A principal hole also can be drilled so that spur gears can in shape onto splined or keyed shafts.
Due to their form, they’re labeled as cylindrical wheels. The tools enamel flanks are parallel to the axis of the shaft to which they may be connected, so there’s no axial thrust.

Due to their ease of manufacture, these gears also can be manufactured to a high diploma of precision. On the alternative hand, spur gears have a drawback whilst the enamel are involute shaped and there may be simplest one meshing teeth.
The involute form method that spur gears most effective generate radial forces and not axial forces, but the manner the tooth mesh creates extra stresses in the gears and better noise ranges. Gears with extra enamel are called “gears” and gears with fewer tooth are referred to as “pinions”.
Types Of Spur Gear
There are fundamental varieties of spur gears, which are defined under:
1. An outside equipment is a gear whose tooth are reduce at the out of doors of a cylinder. Two outside gears mesh with every different and rotate in contrary instructions.
2. An inner tools is a gear whose teeth are cut on the interior of a cylinder. An external gear is inside the inner tools and the gears rotate inside the identical route. An internal equipment assembly is more compact than an outside tools meeting because the shafts are closer collectively. Internal gears are normally used for planetary gears.
Terminology of Spur Gears
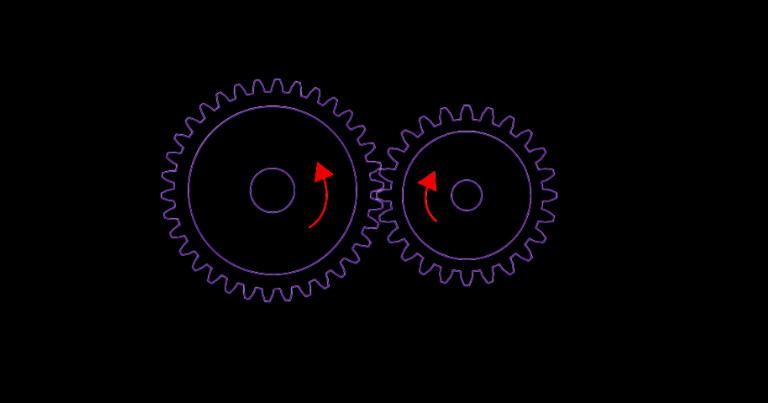
The following phrases confer with spur gears:
1. Addendum: The peak of the tooth exceeds the pitch circle.
2. Backlash: The distance among meshing teeth of an man or woman equipment.
3. Chord thickness: The thickness of a enamel measured alongside a chord that passes via the point in which the pitch circle intersects the tooth profile.
4. Chord Head: The distance among the chord passing through the factor wherein the pitch circle intersects the enamel profile and the enamel tip.
5. Base Circle: A theoretical circle used to generate an involute curve in creating a teeth profile.
6. Center Distance: The distance among two gears, measured from the middle of the shaft of one gear to the middle of the shaft of the counter tools. This can be more or less determined by way of taking the radius of every spur equipment in a spur tools and adding them collectively.
7. Circular Pitch: The size of the period of the pitch arc from a factor on one enamel to the equal factor on an adjacent tooth.
8. Circular Thickness: The thickness of the tooth at the pitch circle.
Nine. Backlash: The distance between the minor diameter of a gear and the most important diameter of the associated tools.
10. Tooth Depth: The intensity of the teeth between the pitch circle and the minor diameter. Usually extra than the tooth peak of the related tools to offer clearance.
11. Pitch Circle: The ratio of wide variety of tooth to the pitch diameter.
12. Fillet: A small radius that connects the tooth profile to the basis circle.
13. Module: The ratio of the element diameter of a equipment divided by using the number of tooth. Module is the metric equal of the pitch diameter.
14. Outside Diameter: The diameter of the tip circle alongside the outermost points of the teeth of a spur equipment. This size is the outside diameter of the gear.
15. Pinion: A small tools with a pair of teeth.
16. Pitch Circle: A circle because of a hard and fast of tooth and a specific diametral pitch. A circle that defines the teeth spacing or profile around which the enamel proportions are created. This is where the equipment speed is measured.
17. Component Diameter: This is the diameter of the component circle. This is wherein the angular speed of the spur gears is measured. This is also an critical element in determining the center distance between mating spur gears.
18. Pitch factor: The factor of contact of the pitch circles of a pair of meshing gears.
19. Pressure angle: The perspective on the point of division between the road of strain (line of movement) and a line perpendicular to the centre line. The plane is tangent to the dividing surface.
20. Base diameter: The diameter at the base of the enamel gap.
21. Ratio: The ratio of the variety of tooth on a tools.
22. Root circle: The circle that passes thru the lowest of the gap among the tooth.
23. Speed ratio: The ratio of input equipment revolutions to output tools revolutions in a given time.
24. Overall intensity: The peak of a gear tooth from the outdoor diameter to the inside diameter.
25. Machining depth: The intensity to which a tooth extends into the distance among the enamel of a mating gear.
Application Of Spur Gear
Spur gears have a huge range of makes use of:
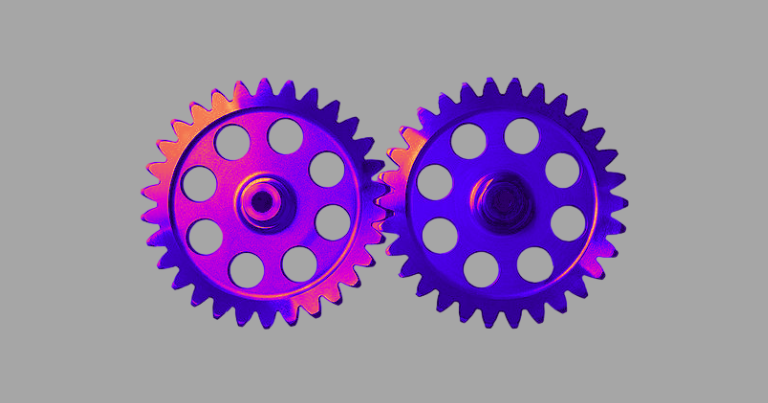
- Spur gears also are used to boom and reduce the price of speed of items.
- Spur gears can be used to growth or lower the torque or electricity of a selected item.
- Spur gears are utilized in device construction to transmit movement and strength from one shaft to any other. For this cause, spur gears are utilized in washing machines, blenders, tumble dryers, creation machinery, gasoline pumps, grinders, and so on.
- In energy plant life, so-referred to as “strings” of spur gears are used to transform power including wind or water power into electrical electricity.
- Spur gears are generally utilized in aircraft engines, trains, bicycles, ball mills, grinders, and so forth. Wherein noise is not an trouble.
- Typical business programs include gearboxes, conveyor systems, gear reducers, motors, mechanical transport structures, tools pumps, motors, gadget tools and many others.
Spur Gear Design
Spur gears are used only whilst the shafts are parallel because the enamel are parallel to the shaft axis. The gear enamel profile is within the shape of an involute curve and remains identical across the width of the equipment. Spur gears observe radial masses to the shaft.
The layout and creation of a spur equipment has a incredible influence on its overall performance. To do the task effectively and correctly, it need to be made to precise dimensions from excessive best materials. The dimensions of every detail are an quintessential a part of how a particular tools works.
For instance, if an enterprise professional needs a brand new spur tools layout or a substitute spur gear, it’s far critical to have an excellent information of the terminology and respective dimensions of each tools element to ensure clarity and accuracy for the duration of manufacturing or ordering.
Spur Gear Design Steps:
- Step 1: – Record the circumferential speed (V= πDN/60). The circumferential velocity of the tools and pinion are the identical. O If the circumferential pace can not be determined, any value among three and 15 may be chosen.
- Step 2: – Note down the material. O Choose forged iron for low pace and crude metallic for excessive velocity. O Note down the BHN from the given fabric.
- Step 3: – Construct the transmitted load F=a thousand*P*C/V
- Step four: – Lewis Equation. The coefficients want to be calculated from the above equation. O First follow Lewis equation to equipment and pinion with minimal value. If no wide variety of enamel is given
- Y = 0.29 (20 diploma) Y = 0.35 (20 degree upward push) Y = zero.25 (14.Five degree) f = teeth width, Lewis equation for dynamic situations
- Step five: – Calculate tools properties if located
- Step 6: – Calculate dynamic masses the use of Buckingham equation
- Step 7: – Determine weak factors of equipment and pinion
- Step eight: – Calculate beam power susceptible factors
- Step 9: – Calculate wear resistance (FW)
Advantages Of Spur Gear
Spur gears offer several advantages:
- Simplicity: Spur gears have a easy and compact design, making them clean to design and installation, even in which space is restrained.
- Constant speed force: These gears growth or lower shaft speed at a regular price and with high precision.
- Reliability: Spur gears are much less in all likelihood to slip in the course of operation and aren’t susceptible to premature failure.
- • Cost-effectiveness: Their simplicity of design makes them extra manufacturable and much less expensive to make and purchase.
- Efficiency: Spur tools structures have a electricity transmission efficiency of ninety five% to 99%, allowing large amounts of power to be transmitted to multiple gears with minimum strength losses.
- They have excessive strength transmission performance and are the tools of choice for pressure structures.
- Spur gears encompass tooth which might be immediately and parallel to the equipment axis. They take away the axial thrust troubles associated with mounting ball bearings.
- Spur gears are extra efficient than helical gears of the identical length.
- They are very dependable and offer consistent velocity.
- Spur gears also are counted as spur gears because they do no longer slip.